EDITOR’S NOTE: This blog post is the first in a three-part series. If you’re considering contract manufacturing services, you’ll want to watch this space. The posts in this series provide a great introduction to who we are, what we do, and why we’re so passionate about creating solutions for our customers. We hope you enjoy these posts and find them useful.
When we acquired Carolina Tool Works in January 2019, one of the first things we did was change the company name to “CST Precision.” We wanted our new name to both reflect and explain our technologies to our customers. We chose “CST” because these letters stand for Combining, Shaping, and Transforming – three key tasks that are at the core of everything we do. In this first blog post of our series, we’re going to focus on the “C.” So let’s take a closer look.
What is “Combining”?
When we talk about “combining” in a contract manufacturing setting, we’re actually referring to several things. We’ll start with the most basic one. At the simplest level, “combining” means we’re using technology to join or mix two materials in order to satisfy a customer’s functional characteristic. Perhaps we need to weld those materials together. Another project might require us to assemble them with bolts or screws. In other cases, we might bond materials to each other. Welding, assembling, and bonding are all examples of combining.
Each of these techniques has its advantages and merits, so which is the right one to use? It really depends on what our customer is trying to accomplish, and whether the setting is a prototype phase or a full production phase. For example, if you’re working on a prototype, you’re probably not terribly concerned about aesthetics at this stage – so welding two components together is a great solution. For some production environments, however, it’s a little different. Maybe you want your finished product to look flawless (or at least as close to it as possible). In that case, welding might not be so appealing if it’s going to be visible to end-users. And in the production phase, you may also not want the added labor that welding requires. On the other hand, welding could be the perfect solution in some production environments because it may be the best way to satisfy cost constraints.
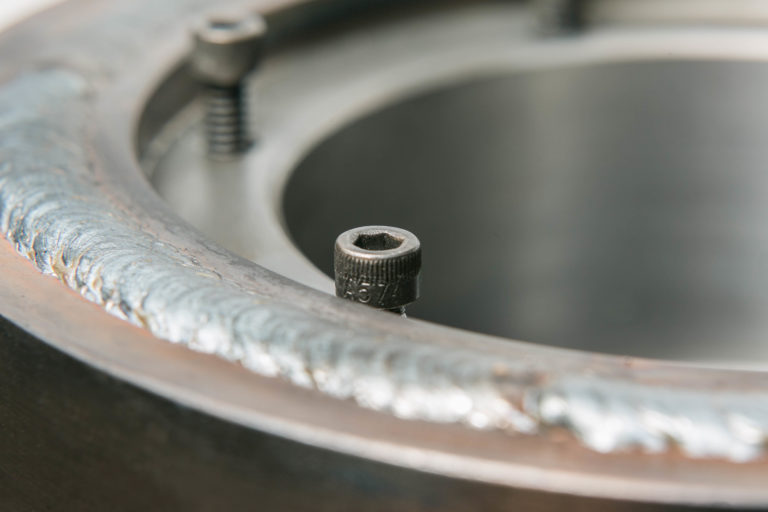
There’s usually never just one right answer, and that’s what makes this industry so fascinating. Take the options that are available with bonding, for instance. There are so many different kinds of bonding glues and technologies we can use. The key is knowing your components, because certain glues can disintegrate over time or during production.
Other Types of Combining
What about if you’re in the printing industry? In that case, “combining” means applying ink to a surface (in order to make that surface readable). The printed surface in question could be a label, a user guide, an insert, or a parts list. But that printed surface could also be objects such as kitchen utensils (think of that Pyrex measuring jug you use all the time), medical equipment, or PVC pipes. You might need to use a specific color of ink for safety reasons. Tasks that most of us take for granted, such as marking an object, could require an incredibly detailed engineering process. It’s important to ensure that the printing ink will adhere to a surface properly and stand up to repeated use, wear, and/or cleaning.
Insert/over molding are two processes that also come under the generic term of “combining.” These processes could include tasks such as putting a handle on a screwdriver blade, or a silicone spatula head over a stainless-steel handle. The nuances and specifics involved in these processes depend on things as varied as ergonomics or safety concerns.
Finally, let’s not forget platings and coatings, which also use combining technologies. Platings and coatings are perfect solutions for customers who need their products to be non-corrosive or to last a long time. (Patio/pool furniture and cookware are everyday examples of items that benefit from platings and coatings.) Deciding which ones to use depends on many factors, especially cost. For instance, combining a less expensive material, such as brass, with a zinc plating or black oxide process could lower the manufacturing cost significantly compared to using a higher-priced material, such as stainless steel.
The bottom line when it comes to your options for combining? There is clearly no “one size fits all” approach. And that’s why we always conduct a detailed consultation with our clients. Together, we explore options, discuss design constraints, understand functional performance requirements, and consider the engineering options. The result is a manufacturing solution that’s tailor-made for you and your situation.
In the second post of this series, we’ll discuss the “S” in CST: shaping. In the meantime, if you’d like to learn more about combining – or CST Precision – please contact us at info@cstprecision.com or 864.879.8165. We’d love to work with you, from concept to prototype, print to part, prototype to production, and production to supply chain fulfillment!