Our New Name Says it All: A Closer Look at CST Precision, Part 2
EDITOR’S NOTE: This post is the second in a three-part series. If you’re considering contract manufacturing services, you’ll want to watch this space. The posts in this series provide a great introduction to who we are, what we do, and why we’re so passionate about creating solutions for our customers. We hope you enjoy these posts and find them useful.
When we acquired Carolina Tool Works in January 2019, one of the first things we did was change the company name to “CST Precision.” We wanted our new name to both reflect and explain our technologies to our customers. We chose “CST” because these letters stand for Combining, Shaping, and Transforming – three value-added activities that are at the core of everything we do. The first post of our series focused on the “C” – combining. In this post, we’ll be discussing the “S,” which stands for shaping. Let’s jump in!
In a contract manufacturing setting, “shaping” simply means starting with raw material and then removing material to achieve a final specification.
There’s no single “right way” to shape something. In fact, there are multiple types of shaping technologies we can use. And that means we can choose the option that’s the best fit for each customer’s unique situations, needs, and budget. Before we can do that, however, we have to ask a few important questions, including:
• How many items do we need to make?
• How soon does the customer need the work done?
• What kind of materials will we be using?
• What are the critical specifications and/or design constraints?
• What are the product’s functional requirements?
Once we know the answers to these questions, we can identify the best technology option for each customer’s circumstances. Depending on your specific requirements, we might use one or more of the following options to get your job done:
• CNC Milling
• CNC Turning
• Electrical Discharge Machine (EDM)
• Laser Machining
• Precision Grinding
• Stamping
• CNC Swiss Manufacturing
• Manual Lathe
• Manual Mills
Let’s look at some of these shaping technologies in a little more detail.
EDM technology is a cost-effective material removal method that allows manufacturers to create features that are often much less expensive to machine, compared to traditional machining processes like milling and turning. The EDM method creates special features into a part and can be used to produce both small and large quantities. Let’s say you need to cut a keyway into a single pulley or gear to fit with a mating shaft. Historically, using a broach would produce the result you wanted, but it would also require a tool to create the specific-sized keyway. EDM, on the other hand, offers you a much more economical method to get the job done, while taking advantage of superior technology. That’s because an EDM machine provides the versatility to make any sized keyway without the expense of maintaining a tooling inventory.
Laser Machining. Technology for shaping metal has come a long way, and it continues to make significant advances. Laser machining, for example, allows us to create parts quickly and accurately without needing to create custom punches and dies. Lasers are also adaptive: We can use them to cut features and shapes into tubes, which has drastically enabled progress in the medical stent market. Products that were previously conceptual are now a reality, because lasers have overcome many limitations of traditional machines and tools.
Precision Grinding is a shaping technology we can use to achieve extremely tight tolerances and fine surface finishes. Grinding itself is an old technology. Shafts, bearings, and various tooling are all traditional examples of ground components. But precision grinding’s capabilities continue to improve in response to market demands. Medical device components, for instance—specifically, the guidewires used for minimally invasive procedures—have advanced grinding capabilities. The tools that are produced as a result are improving the quality of life for patients and surgeons around the world.
CNC Swiss Manufacturing is similar to that of a CNC Lathe, but it’s more specialized for repeatability and volume. Enhancements in machine design have made these machines even more friendly to the prototype process. Historically, CNC Swiss-style machines were ideal for high-volume, continuous production of screws and similar items, and they still are well suited for this type of product. But technology advancements in Swiss Machining have also resulted in machines that are now capable of producing a much greater variety of parts in single operations, thanks to the addition of spindles, lasers, and multiple axes.
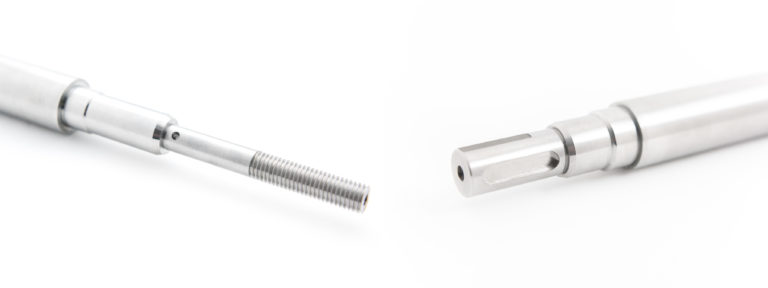
Because there is no “one size fits all” approach when it comes to shaping, we always conduct a detailed consultation with our clients. Together, we explore options, discuss design constraints, understand functional performance requirements, and consider all manufacturing options. The result is a manufacturing solution that’s tailor-made for you and your situation.
In the third post of this series, we’ll discuss the “T” in CST: transforming. In the meantime, if you’d like to learn more about shaping – or CST Precision – please contact us at info@cstprecision.com or 864-879-8165. We’d love to work with you, from concept to prototype, print to part, prototype to production, and production to supply chain fulfillment!