Our New Name Says it All: A Closer Look at CST Precision, Part 3
EDITOR’S NOTE: This post is the third in a three-part series. If you’re considering contract manufacturing services, you’ll want to watch this space. The posts in this series provide a great introduction to who we are, what we do, and why we’re so passionate about creating solutions for our customers. We hope you enjoy these posts and find them useful.
When we acquired Carolina Tool Works in January 2019, one of the first things we did was change the company name to “CST Precision.” We wanted our new name to both reflect and explain our technologies to our customers. We chose “CST” because these letters stand for Combining, Shaping, and Transforming – three key tasks that are at the core of everything we do. The first post of our series focused on the “C” – combining. In the second post, we discussed the “S,” which stands for shaping. For today’s post, we’ll be taking a closer look at the “T”. It’s time to talk about transforming!
Transforming is a critical operation in manufacturing. Lots of commodity items that we touch and encounter – and take for granted – on a daily basis benefit from transforming. When it’s done right, we don’t even notice or appreciate the chemistry and physics that are involved. It’s really not that different from the experience of eating out at an upscale restaurant. You can obviously recognize that the chef has fantastic recipes and knows all the inputs which need to be managed in order to produce the output (namely, that fantastic gourmet meal sitting on your plate). Although you may not be able to eat the results of our work, it’s just as interesting to learn a little more about what’s cooking behind the scenes.
One of the most common transformation processes we use here at CST Precision is the heat treatment process. During heat treatment, we harden or soften something (typically metals or plastics) so that it performs better. Take cutting blades, for example. By hardening them with heat treatment, we can make those blades do a much better job than they would if we didn’t harden them. They’ll last longer, cut more precisely, and be more durable.
Conversely, when we use heat treatment to soften a material, we make it more machinable and malleable, which means we can then bend it and mold it. This is frequently done with electrical connectors that are machined from brass or copper. With these jobs, we’ll use a heat treatment process called annealing. Think of that electrical connector as a tube that needs to fasten onto something. In order for that to happen, you need to crimp, squeeze, or crush that tube. If it’s not annealed first, it’s going to be brittle and it’s likely to crack. But annealing that tube before we do anything else changes the game: The annealed connector becomes soft and malleable, enabling us to shape it and create the pressure which, in turn, creates the connection.
As we mentioned earlier, heat treatment isn’t just for metals. It’s also useful for plastics that need to be softened. Let’s say we’ve just extruded a plastic tube. That general process results in an object that’s somewhat rigid. But if we put that same tube into an oven to anneal it, we can soften it and give it more desirable characteristics (such as increased malleability).
Two other transforming processes that we use frequently are etching and laser engraving. With these, we can put identifying or graduated marks onto many different kinds of objects, including medical instruments and devices, or measuring equipment (such as rulers). Etching is a very controlled and extremely precise chemical process that uses acid to burn, char, or scorch the marks right onto the material. Laser engraving is slightly different, because it uses a controlled light beam (laser) to make marks.
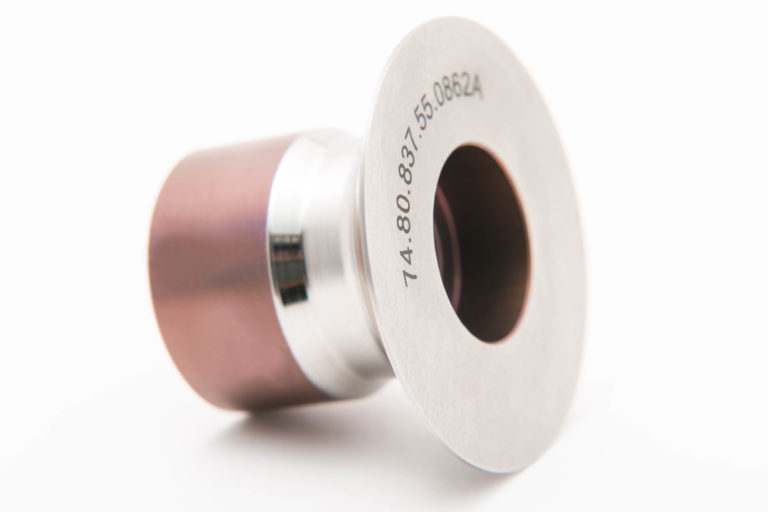
Another transforming process that we have available to our customers is passivation. You can think of this technique as being rather like a cleaning process. It’s a great option for stainless steel. We often think of this material as being corrosion resistant, and for the most part it is. But we can increase that resistance by putting the material through passivation. This involves placing the stainless steel into an acidic bath that strips and removes all of the iron from the surface. The result? Maximum rust prevention and corrosion resistance.
Whether it’s heat treatment, annealing, etching, laser engraving, or passivation, the transforming work we do typically happens after the combining and shaping operations are complete. Sometimes, transforming work might occur in the middle of different shaping operations. Unlike combining and shaping, our transforming processes are rarely standalone; they are a value-added service, typically in addition to combining and shaping.
As with combining and shaping, there is no “one size fits all” approach when it comes to transforming. That’s why we always conduct a detailed consultation with our clients. Together, we explore options, discuss design constraints, understand functional performance requirements, and consider all manufacturing options. The result is a manufacturing solution that’s tailor-made for you and your situation.
To learn more about transforming – or CST Precision – please contact us at info@cstprecision.com or 864-879-8165. We’d love to work with you, from concept to prototype, print to part, prototype to production, and production to supply chain fulfillment!